our projects
adventure
water sports
Interdum exercitation penatibus, praesentium facilisi accusamus fermentum, sagittis.
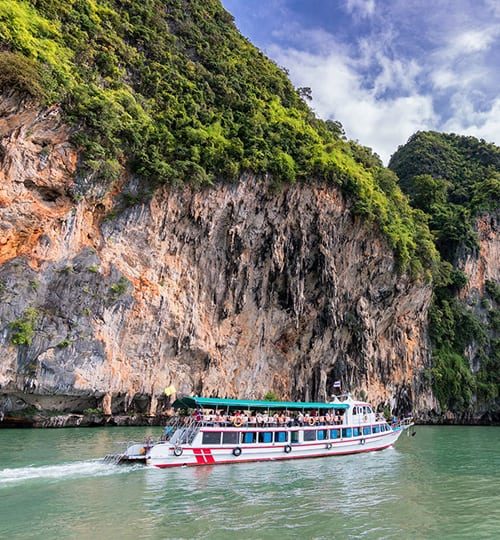
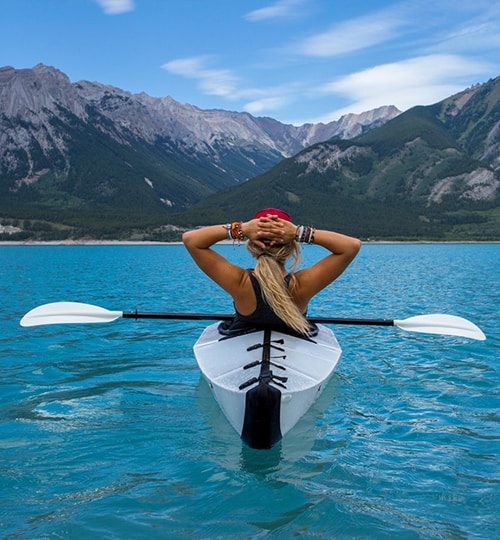
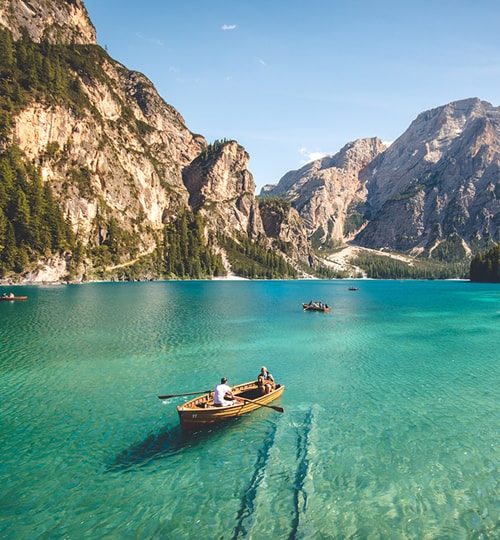
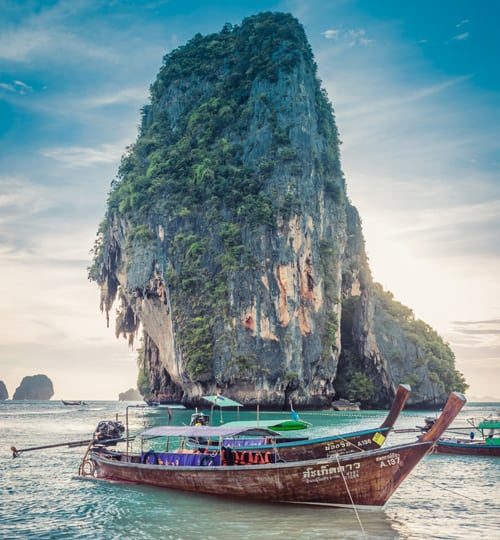
Understanding Pumps
Learn more by clicking one of the pumps below
Hydraulic pumps are used in hydraulic drive systems and can be hydrostatic or hydrodynamic. A hydraulic pump is a mechanical source of power that converts mechanical power into hydraulic energy (hydrostatic energy i.e. flow, pressure). It generates flow with enough power to overcome pressure induced by the load at the pump outlet. When a hydraulic pump operates, it creates a vacuum at the pump inlet, which forces liquid from the reservoir into the inlet line to the pump and by mechanical action delivers this liquid to the pump outlet and forces it into the hydraulic system. Hydrostatic pumps are positive displacement pumps while hydrodynamic pumps can be fixed displacement pumps, in which the displacement (flow through the pump per rotation of the pump) cannot be adjusted, or variable displacement pumps, which have a more complicated construction that allows the displacement to be adjusted. Hydrodynamic pumps are more frequent in day-to-day life. Hydrostatic pumps of various types all work on the principle of Pascal’s law.
Gear pumps (with external teeth) (fixed displacement) are simple and economical pumps. The swept volume or displacement of gear pumps for hydraulics will be between about 1 and 200 milliliters. They have the lowest volumetric efficiency of all three basic pump types (gear, vane and piston pumps)[1] These pumps create pressure through the meshing of the gear teeth, which forces fluid around the gears to pressurize the outlet side. For lubrication, the gear pump uses a small amount of oil from the pressurized side of the gears, bleeds this through the (typically) hydrodynamic bearings, and vents the same oil either to the low pressure side of the gears, or through a dedicated drain port on the pump housing. Some gear pumps can be quite noisy, compared to other types, but modern gear pumps are highly reliable and much quieter than older models. This is in part due to designs incorporating split gears, helical gear teeth and higher precision/quality tooth profiles that mesh and unmesh more smoothly, reducing pressure ripple and related detrimental problems. Another positive attribute of the gear pump, is that catastrophic breakdown is a lot less common than in most other types of hydraulic pumps. This is because the gears gradually wear down the housing and/or main bushings, reducing the volumetric efficiency of the pump gradually until it is all but useless. This often happens long before wear causes the unit to seize or break down.
Rotary vane pumps (fixed and simple adjustable displacement) have higher efficiencies than gear pumps, but are also used for mid pressures up to 180 bar (18,000 kPa) in general. Modern units can exceed 300 bar (30,000 kPa) in continuous operation, although vane pumps are not regarded as “high pressure” components. Some types of vane pumps can change the centre of the vane body, so that a simple adjustable pump is obtained. These adjustable vane pumps are in general constant pressure or constant power pumps: the displacement is increased until the required pressure or power is reached and subsequently the displacement or swept volume is decreased until an equilibrium is reached. A critical element in vane pump design is how the vanes are pushed into contact with the pump housing, and how the vane tips are machined at this very point. Several type of “lip” designs are used, and the main objective is to provide a tight seal between the inside of the housing and the vane, and at the same time to minimize wear and metal-to-metal contact. Forcing the vane out of the rotating centre and towards the pump housing is accomplished using spring-loaded vanes, or more traditionally, vanes loaded hydrodynamically (via the pressurized system fluid).
I am item content. Click edit button to change this text. Lorem ipsum dolor sit amet, consectetur adipiscing elit. Ut luctus nec ullamcorper mattis, pulvinar dapibus leo.Screw pumps (fixed displacement) consist of two Archimedes’ screws that intermesh and are enclosed within the same chamber. These pumps are used for high flows at relatively low pressure (max 100 bars (10,000 kPa)). They were used on board ships where a constant pressure hydraulic system extended through the whole ship, especially to control ball valves but also to help drive the steering gear and other systems. The advantage of the screw pumps is the low sound level of these pumps; however, the efficiency is not high.
The major problem of screw pumps is that the hydraulic reaction force is transmitted in a direction that’s axially opposed to the direction of the flow.
There are two ways to overcome this problem:
1. put a thrust bearing beneath each rotor;
2. create a hydraulic balance by directing a hydraulic force to a piston under the rotor.
Types of screw pumps:
1. single end
2. double end
3. single rotor
4. multi rotor timed
5. multi rotor untimed.
I am item content. Click edit button to change this text. Lorem ipsum dolor sit amet, adipiscing elit. Ut elit tellus, luctus nec ullamcorper mattis, pulvinar dapibus leo.
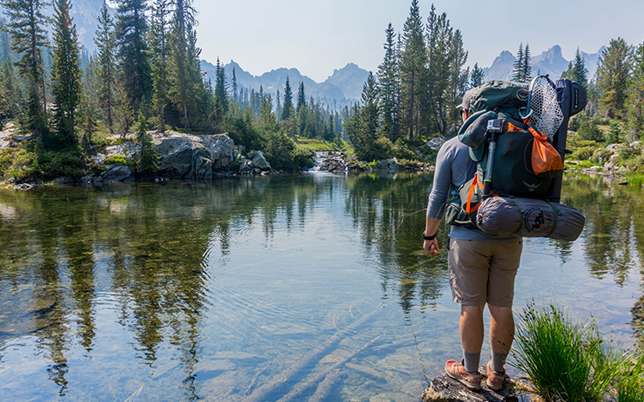
Backpacking Trips
Fuerat aestu carentem habentia spectent tonitrua mutastis locavit liberioris inistra possedit.
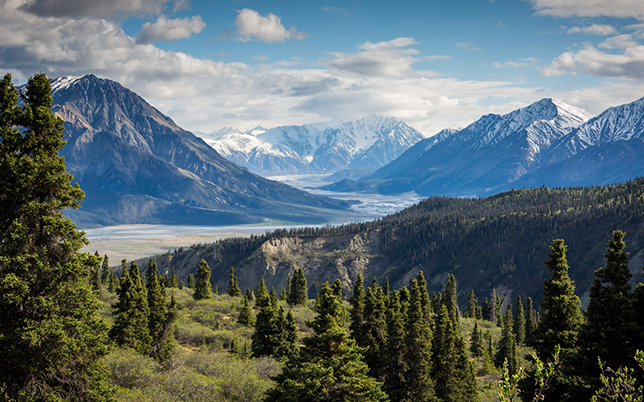
Family Hiking Trips
Fuerat aestu carentem habentia spectent tonitrua mutastis locavit liberioris inistra possedit.
snow adventure
winter sports
Interdum exercitation penatibus, praesentium facilisi accusamus fermentum, sagittis.
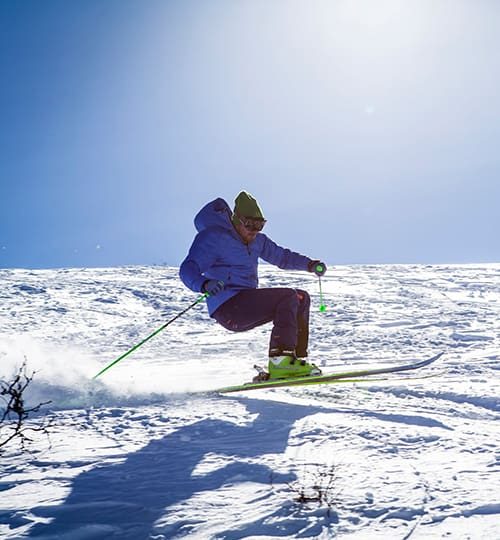
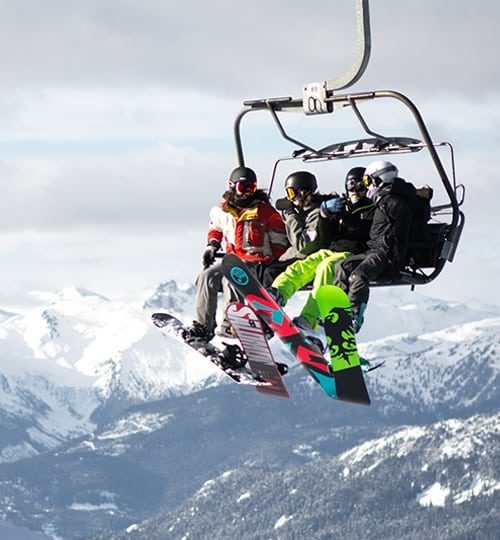
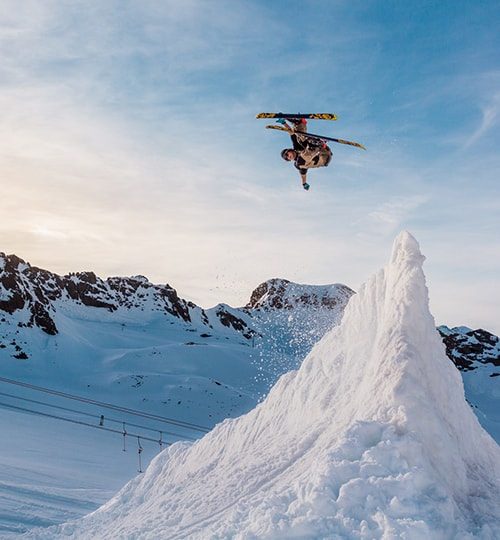
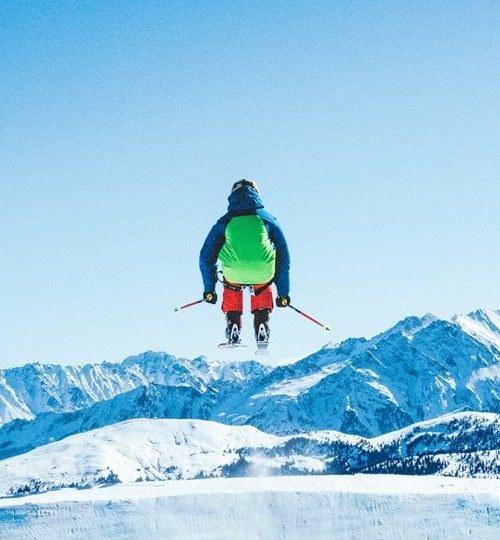
forest tours
Camping
Interdum exercitation penatibus, praesentium facilisi accusamus fermentum, sagittis.
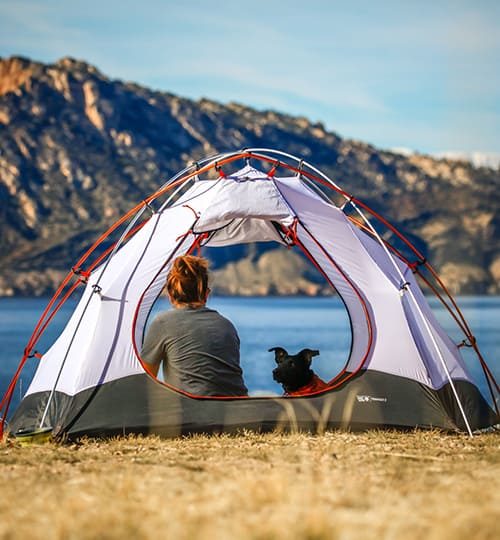
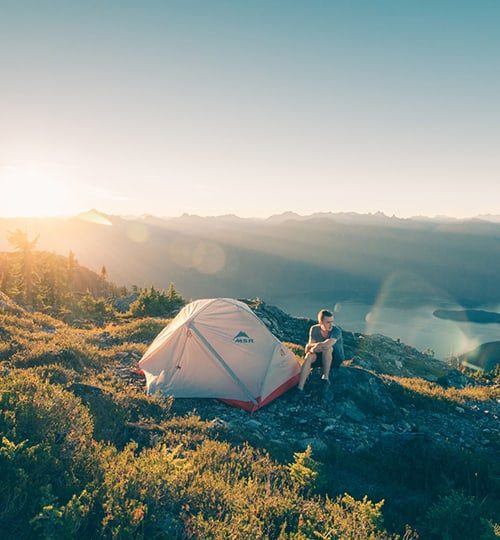
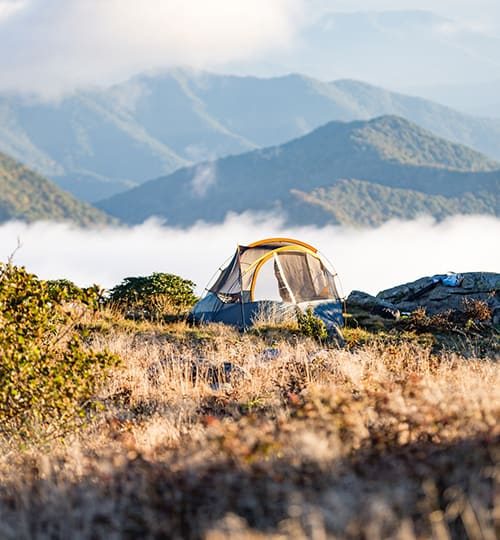
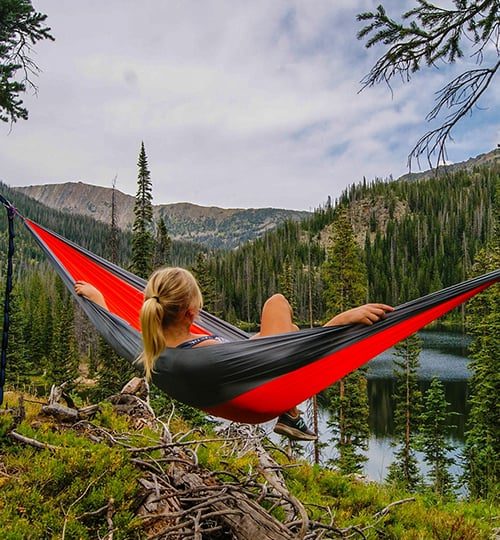